Near Net Molding
Near Net Molding
SADM/SPMM Process:
At the forefront of innovation, our SADM (Specialized Advanced Developmental Materials) Precision Molding & Machining (SPMM) process exemplifies efficiency, precision, and cost-effectiveness in the manufacturing of advanced materials. This proprietary process leverages near net shaping to dramatically reduce waste and cost, particularly when handling hazardous materials like lead.
Key Benefits:
Near Net Shaping: Our technique ensures that the initial cast form is as close to the final required shape as possible, reducing the amount of material waste and machining time.
Hazardous Material Handling: By minimizing the amount of material that needs to be machined away, we reduce the exposure and cost associated with disposing of hazardous materials.
Cost Savings: Significant reductions in material and machining costs translate into savings for our customers.

Success Stories:
General Dynamics and the US Navy: We recently collaborated with General Dynamics to create a simple ring mold for the US Navy. This innovative approach saved the Navy approximately half a million dollars by opting for near net molding over purchasing a panel and machining the ring. This is just one of many success stories that highlight the value of our SADM/SPMM process.
Lockheed Martin and the LWLC Upgrade: In a recent project with Lockheed Martin, we contributed to the Lightweight Low-Cost (LWLC) upgrade of their sonar system. Using our proprietary syntactic materials, SADM .5 and BCF 40b, we developed a lightweight hydrophone baffle housing. The outer shell, made of SADM, and the middle layer of BCF 40b provide both strength and light weight. This exclusive process makes us the sole supplier of these critical components for Virginia-class submarines, exemplifying our commitment to innovation and excellence in advanced materials.
Click the images below to enlarge.
Reduce cost of acoustic foam parts with near-net molding
A major reason for developing the new technology was to reduce cost and waste when machining finished parts from acoustic material containing heavy metals and unique polymers. “The molds are inexpensive, since we are only molding a near-net shape that will be machined after molding,” said Bruce St. Hilaire.
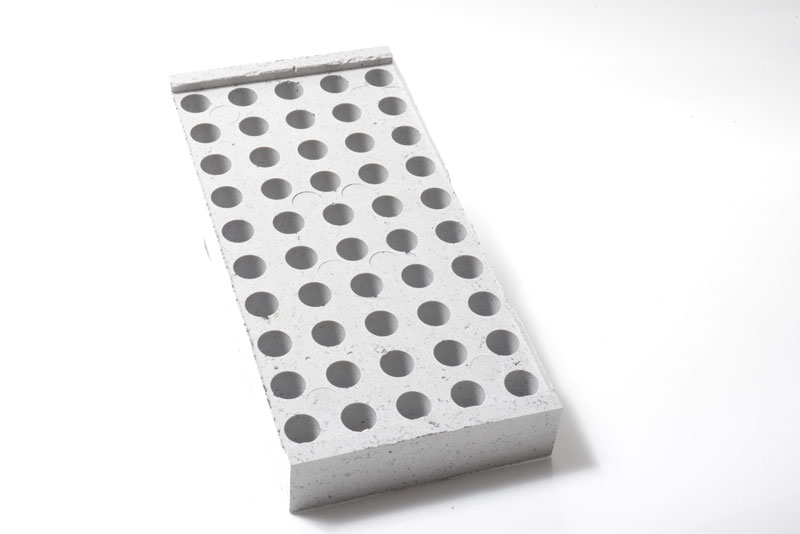
Raw Molded Part
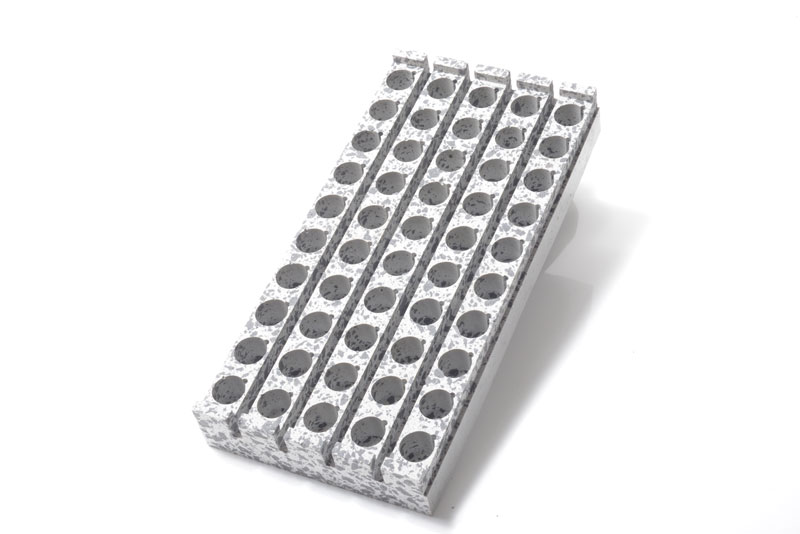
After Machining
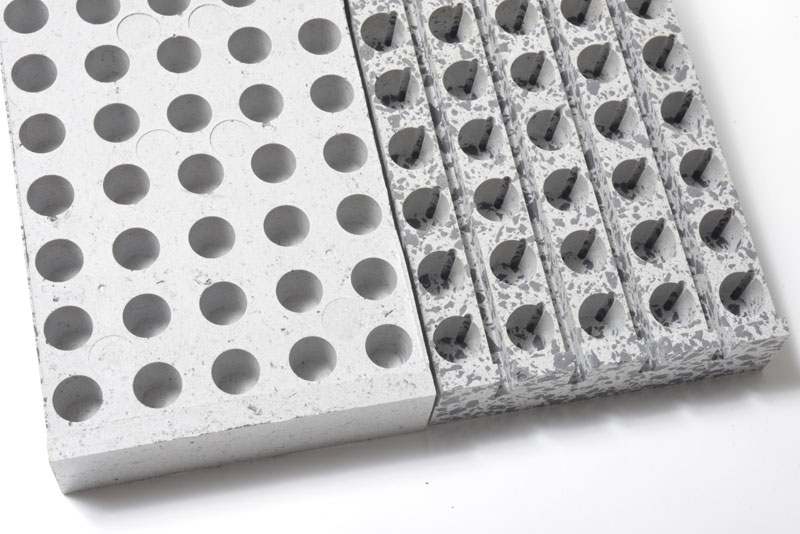
Before/After Machining
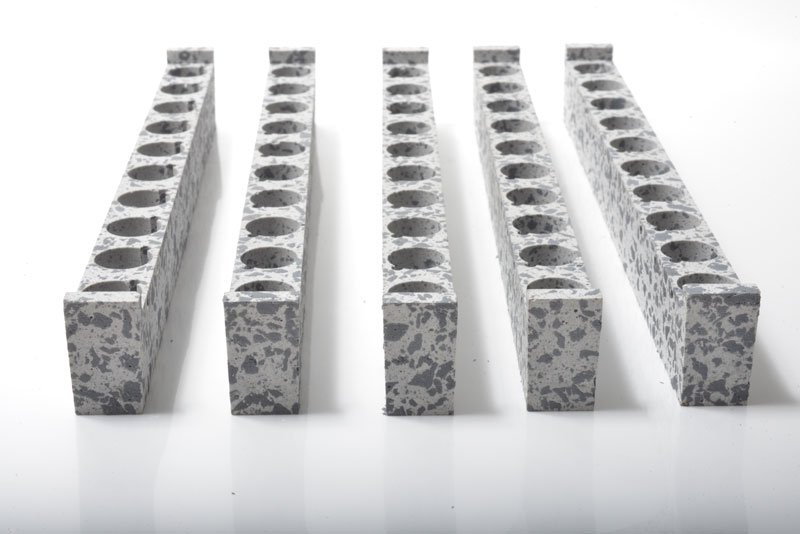
Finished Product
Complex custom parts in less time
The technology allows Suburban Machine to offer small batch runs of these acoustic foams. This in turn allows Suburban Machine to offer foams with different compositions and different application methods, such as Tactically Distributed foams and Direct Application foams. There is no need to settle for off the shelf materials when Suburban Machine can create the perfect material to result in a superior final product.
The process is suitable for large parts and weights of up to 20 pounds per blank, with large and varying wall thicknesses and complex geometries. Near-net shape is effective for parts that cannot be efficiently produced using standard machining methods due to the greatly reduced machining time.

Greener production process is eco-friendly
“Because it’s close to the final part, a near-net shape requires less machining. Less machining means less waste, which is an important consideration for green and sustainable programs.
With ever changing regulations it is more important than ever to find ways to produce parts in a way that produces less waste and minimizes environmental impact.
To learn more about Suburban Machine’s near-net molding process call 978.392.9100 or contact us via email.